Details
New series with 5kHz high-speed response & noise resistance digital output!
●17 different capacities ranging from 0.05Nm to 10000Nm.
●Analog bandwidth 5kHz with high-speed sampling rate of 20kHz.
●Safe overload of 500%
●Power supply DC24V
●Rated torque at ±10V
●Digital zero function via external signal
●Digital output via RS-485
●Equipped with pulse output for rotation detection
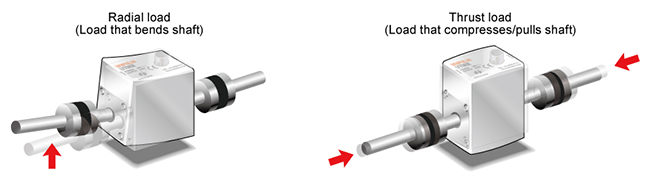
Increased resistance to radial & thrust load
Influences that radial and thrust loads exert on effective accuracy were dramatically reduced.
■Why is load other than torque applied at torque meter?
For torque measurement, when interlocking shafts, misalignments on shaft center as illustrated below occurs by all means.
The devices that absorb radial and thrust loads caused by such misalignments are couplings. However, even the couplings cannot completely absorb such radial and thrust loads, resulting in an impact on torque measurement.
Major misalignments when mounting shafts
Major misalignments when mounting shafts
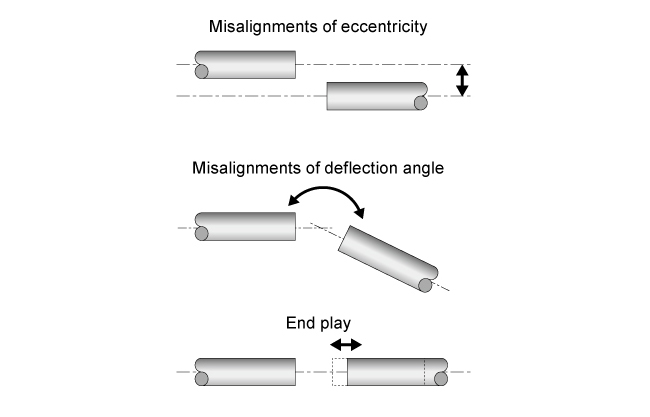
Experimental data
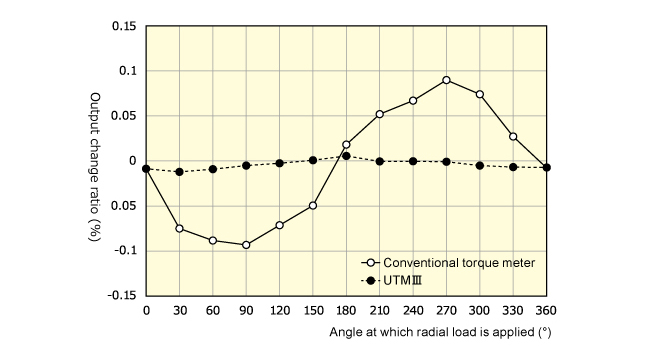
Above illustration shows the output change when one shaft end of UTMIII-2Nm is fixed, and 7N radial load is applied at another shaft end through the bearing.
Output changes depending on rotation angle.
While output value changes 0.1% at maximum with conventional torque meter, output value changes less than 0.01% with UTMIII.
Abundant options available
Abundant options available
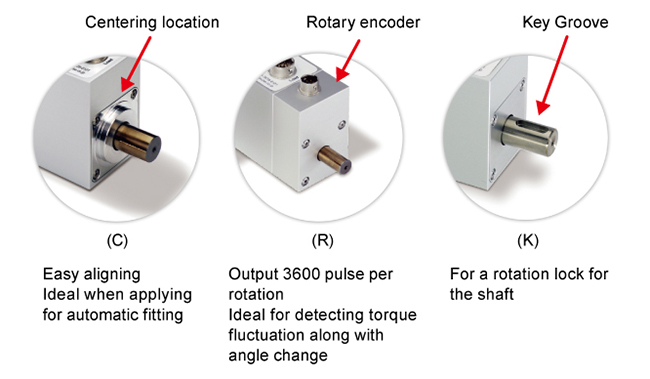
More compact for side-by-side measurement
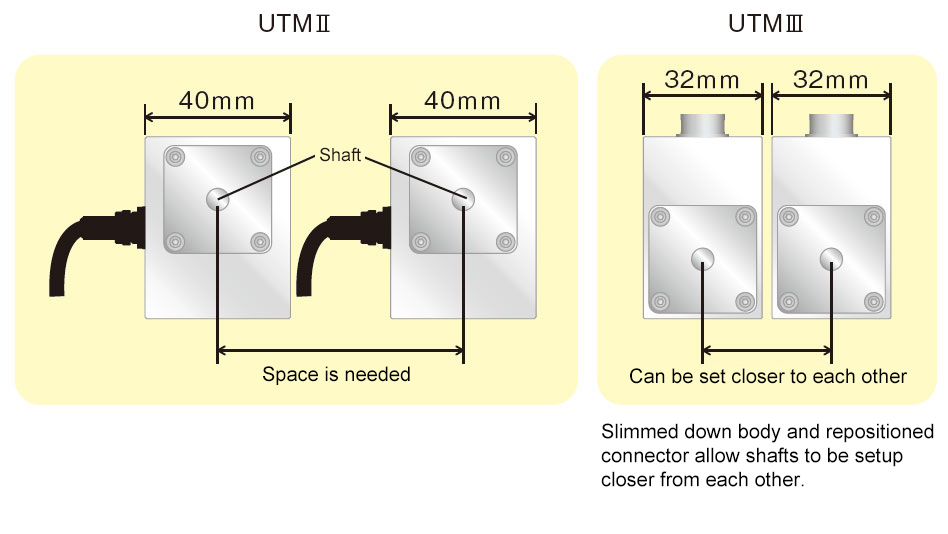
Added zero correction function with external signal
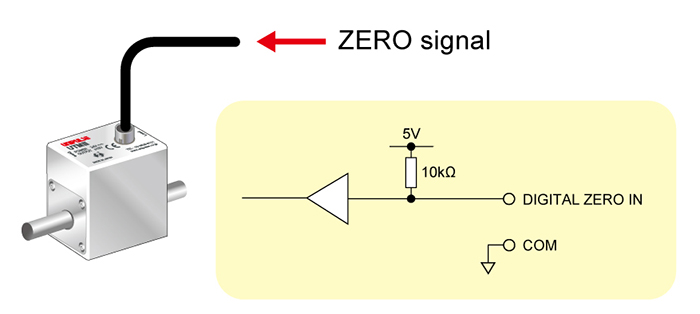
Frequency bandwidth of 5kHz, variable filter
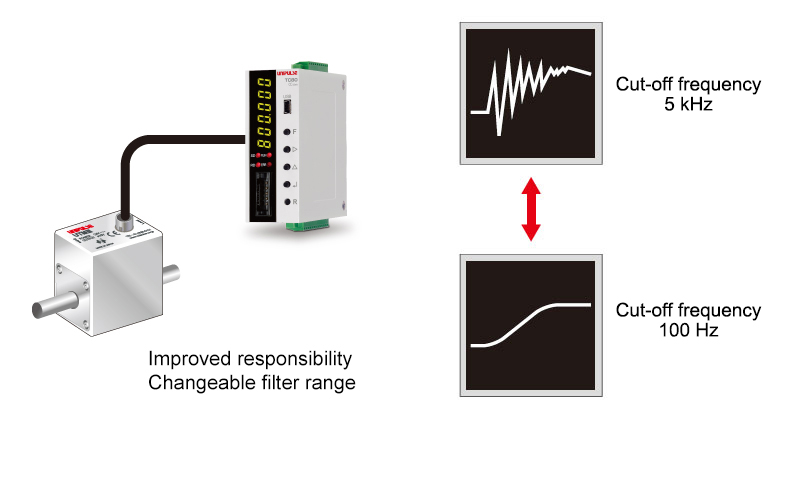
Digital output via RS-485
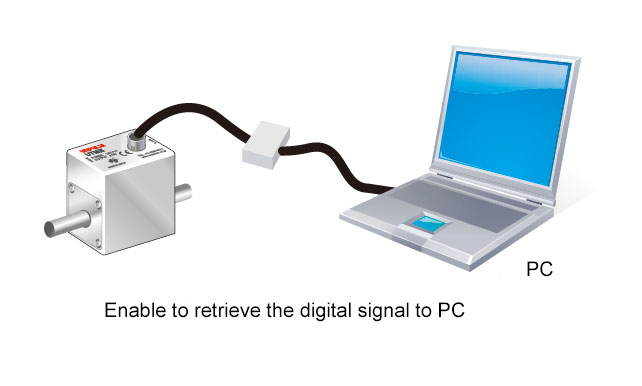
Connection example
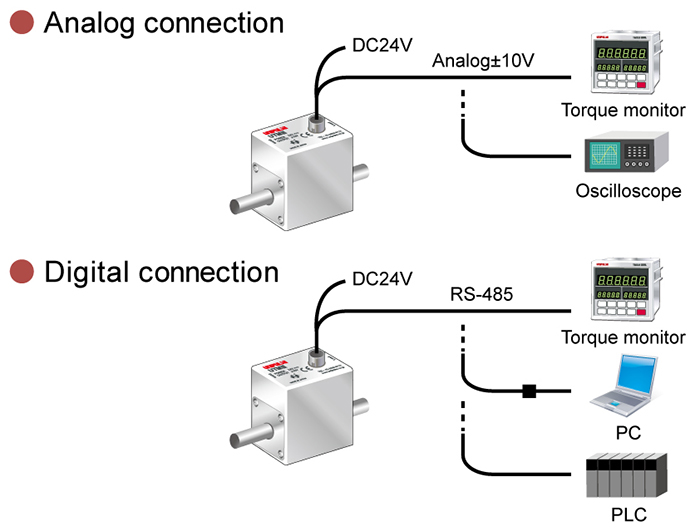
Sample application
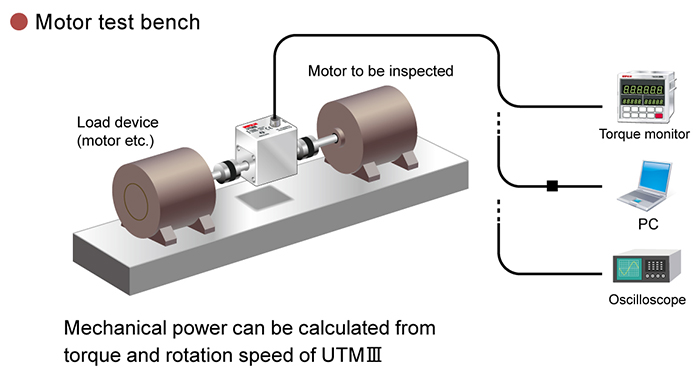
Specifications
» Measurement range:±0.05Nm to ±2Nm
» Measurement range:±5Nm to ±200Nm
» Measurement range:±500Nm to ±10000Nm
» Measurement range:±5Nm to ±200Nm
» Measurement range:±500Nm to ±10000Nm
±0.05Nm to ±2Nm
Measurement range |
±0.05 Nm |
±0.1Nm | ±0.2Nm | ±0.5Nm | ±1Nm | ±2Nm |
---|---|---|---|---|---|---|
Power supply | DC24V ±15% | |||||
Consumption current | 100mA or less | |||||
Output range | ±10V DC Load resistance must be more than 5kΩ | |||||
Responsivity | 5kHz | |||||
Rotation signal |
4 pulses per 1 rotation *1 Open collector Max. ratings 30V, 10mA |
|||||
Digital filter | 1Hz to 1kHz(Depending on settings) PASS 5kHz | |||||
Safe overload | 500%FS | |||||
Non-linearity | 0.03%FS or less | |||||
Hysteresis | 0.03%FS or less | |||||
Repeatability | 0.03%FS or less | |||||
Operation temp. range |
-10 to +50℃ | |||||
Temp. effect on ZERO | 0.01%FS/℃ or below | |||||
Temp. effect on span | 0.01%FS/℃ or below | |||||
Max. rotation speed | 25000rpm | |||||
Torsional spring constant |
5.67 Nm/rad |
11.57 Nm/rad |
26.10 Nm/rad |
93.1 Nm/rad |
188 Nm/rad |
414 Nm/rad |
Maximum torsional angle |
8.81× 10-3rad (0.505°) |
8.64× 10-3rad (0.495°) |
7.66× 10-3rad (0.439°) |
5.37× 10-3rad (0.308°) |
5.32× 10-3rad (0.305°) |
4.83× 10-3rad (0.277°) |
Inertia moment |
8.48× 10-7 kgm2 |
8.58× 10-7 kgm2 |
8.7× 10-7 kgm2 |
1.46× 10-6 kgm2 |
1.49× 10-6 kgm2 |
1.39× 10-6 kgm2 |
Ext. dimension (case size/ W×H×D) |
54×49×32mm | |||||
Total length | 74mm | 84mm | ||||
Shaft diameter |
φ5mm | φ8mm | ||||
Weight | Approx. 140g | Approx. 160g | ||||
Supplied cable |
12-conductor flexible cable (2m) Cable end: 5 wires → Cable length is switchable to 5m(Option:UTMⅢ-L5) |
|||||
Optionally available cable |
CATM351:12-conductor flexible cable (5m) Cable end: 5 wires CATM312:12-conductor flexible cable (10m) Cable end: 5 wires |
|||||
CE marking certificatio |
EMC directives EN61326-1,EN61326-2-3 |
Permissible shaft end load *2
Measurement range |
±0.05Nm | ±0.1Nm | ±0.2Nm | ±0.5Nm | ±1Nm | ±2Nm |
---|---|---|---|---|---|---|
RadialN | 0.12N | 0.25N | 0.3N | 0.5N | 1N | 8N |
ThrustN | 3N | 4N | 5N | 6N | 8N | 30N |
RadialN (R, RC, RK, RCK) |
0.07N | 0.14N | 0.17N | 0.3N | 0.6N | 5N |
ThrustN (R, RC, RK, RCK) |
3N | 4N | 5N | 6N | 8N | 30N |
Option
Measurement range |
±0.05Nm | ±0.1Nm | ±0.2Nm | ±0.5Nm | ±1Nm | ±2Nm |
---|---|---|---|---|---|---|
Key Groove | ||||||
Rotary encoder | ○ | ○ | ○ | ○ | ○ | ○ |
Key groove & Rotary encoder |
||||||
Centering location |
○ | ○ | ○ | ○ | ○ | ○ |
Key groove & Centering location |
||||||
Rotary encoder & Centering location |
○ | ○ | ○ | ○ | ○ | ○ |
Key groove & Rotary encoder & Centering location |
*1 0.05 to 10Nm model can be changed to 60 pulses in 1 rotation specification. Contact us for more details.
*2 Radial N and Thrust N of permissible shaft end load are the values guaranteeing that influence for torque output is less than 0.03% when those loads apply.
*2 Radial N and Thrust N of permissible shaft end load are the values guaranteeing that influence for torque output is less than 0.03% when those loads apply.
±5Nm~±200Nm
Measurement range |
±5Nm | ±10Nm | ±20Nm | ±50Nm | ±100Nm | ±200Nm |
---|---|---|---|---|---|---|
Power supply | DC24V ±15% | |||||
Consumption current | 100mA or less | 150mA or less | ||||
Output range | ±10V DC Load resistance must be more than 5kΩ | |||||
Responsivity | 5kHz | |||||
Rotation signal |
4 pulses per 1 rotation *1 Open collector Max. ratings 30V, 10mA |
|||||
Digital filter | 1Hz to 1kHz(Depending on settings) PASS 5kHz | |||||
Safe overload | 500%FS | |||||
Non-linearity | 0.03%FS or less | |||||
Hysteresis | 0.03%FS or less | |||||
Repeatability | 0.03%FS or less | |||||
Operation temp. range |
-10 to +50℃ | |||||
Temp. effect on ZERO | 0.01%FS/℃ or below | |||||
Temp. effect on span | 0.01%FS/℃ or below | |||||
Max. rotation speed | 25000rpm | 20000rpm | 15000 rpm |
12000 rpm |
||
Torsional spring constant |
691 Nm/rad |
1851 Nm/rad |
5386 Nm/rad |
8428 Nm/rad |
17.3× 103 Nm/rad |
41.7× 103 Nm/rad |
Maximum torsional angle |
7.24× 10-3rad (0.415°) |
5.40× 10-3rad (0.310°) |
3.71× 10-3rad (0.213°) |
5.93× 10-3rad (0.340°) |
5.78× 10-3rad (0.331°) |
4.79× 10-3rad (0.275°) |
Inertia moment |
3.56× 10-6 kgm2 |
3.66× 10-6 kgm2 |
2.59× 10-5 kgm2 |
2.66× 10-5 kgm2 |
6.59× 10-5 kgm2 |
1.40× 10-4 kgm2 |
Ext. dimension (case size/ W×H×D) |
57×54×37mm | 70×63×47mm | 67× 63.5× 56mm |
67×68× 61mm |
||
Total length | 97mm | 150 mm |
170 mm |
177mm | 187mm | |
Shaft diameter |
φ12mm | φ20mm | φ25mm | φ30mm | ||
Weight | Approx. 250g | Approx. 670g | Approx. 1.1kg |
Approx. 1.4kg |
||
Supplied cable |
12-conductor flexible cable (2m) Cable end: 5 wires → Cable length is switchable to 5m(Option:UTMⅢ-L5) |
|||||
Optionally available cable |
CATM351:12-conductor flexible cable (5m) Cable end: 5 wires CATM312:12-conductor flexible cable (10m) Cable end: 5 wires |
|||||
CE marking certificatio |
EMC directives EN61326-1,EN61326-2-3 |
Permissible shaft end load *2
Measurement range |
±5Nm | ±10Nm | ±20Nm | ±50Nm | ±100Nm | ±200Nm |
---|---|---|---|---|---|---|
RadialN | 15N | 20N | 23N | 60N | 90N | 160N |
ThrustN | 40N | 100N | 360N | 400N | 500N | 800N |
RadialN (R, RC, RK, RCK) |
7N | 13N | 20N | 25N | 60N | 100N |
ThrustN (R, RC, RK, RCK) |
40N | 100N | 360N | 400N | 500N | 800N |
Option
Measurement range |
±5Nm | ±10Nm | ±20Nm | ±50Nm | ±100Nm | ±200Nm |
---|---|---|---|---|---|---|
Key Groove | ○ | ○ | ○ | ○ | ○ | ○ |
Rotary encoder | ○ | ○ | ○ | ○ | ○ | ○ |
Key groove & Rotary encoder |
○ | ○ | ○ | ○ | ○ | ○ |
Centering location |
○ | ○ | ○ | ○ | ○ | ○ |
Key groove & Centering location |
○ | ○ | ○ | ○ | ||
Rotary encoder & Centering location |
○ | ○ | ○ | ○ | ○ | ○ |
Key groove & Rotary encoder & Centering location |
○ | ○ | ○ | ○ |
*1 0.05 to 10Nm model can be changed to 60 pulses in 1 rotation specification. Contact us for more details.
*2 Radial N and Thrust N of permissible shaft end load are the values guaranteeing that influence for torque output is less than 0.03% when those loads apply.
*2 Radial N and Thrust N of permissible shaft end load are the values guaranteeing that influence for torque output is less than 0.03% when those loads apply.
±500Nm~±10000Nm
Measurement range |
±500Nm | ±1000Nm | ±2000Nm | ±5000Nm | ±10000Nm |
---|---|---|---|---|---|
Power supply | DC24V ±15% | ||||
Consumption current | 150mA or less |
180mA or less | |||
Output range | ±10V DC Load resistance must be more than 5kΩ | ||||
Responsivity | 5kHz | ||||
Rotation signal |
4 pulses per 1 rotation *1 Open collector Max. ratings 30V, 10mA |
||||
Digital filter | 1Hz to 1kHz(Depending on settings) PASS 5kHz | ||||
Safe overload | 500%FS | ||||
Non-linearity | 0.03%FS or less | ||||
Hysteresis | 0.03%FS or less | ||||
Repeatability | 0.03%FS or less | ||||
Operation temp. range |
-10 to +50℃ | ||||
Temp. effect on ZERO | 0.01%FS/℃ or below | ||||
Temp. effect on span | 0.01%FS/℃ or below | ||||
Max. rotation speed | 10000 rpm |
7000rpm | 6000rpm | 5000rpm | 4000rpm |
Torsional spring constant |
117×103 Nm/rad |
377×103 Nm/rad |
717×103 Nm/rad |
1649×103 Nm/rad |
3255×103 Nm/rad |
Maximum torsional angle |
4.28× 10-3rad (0.246°) |
2.65× 10-3rad (0.152°) |
2.79× 10-3rad (0.160°) |
3.03× 10-3rad (0.174°) |
3.07× 10-3rad (0.176°) |
Inertia moment |
4.70× 10-4 kgm2 |
2.90× 10-3 kgm2 |
5.89× 10-3 kgm2 |
2.01× 10-2 kgm2 |
5.16× 10-2 kgm2 |
Ext. dimension (case size/ W×H×D) |
67×78× 71mm |
86×103× 98mm |
86×119× 111mm |
97×141× 137mm |
103×166× 162mm |
Total length | 217mm | 286mm | 306mm | 387mm | 447mm |
Shaft diameter |
φ40mm | φ60mm | φ70mm | φ90mm | φ110mm |
Weight | Approx. 2.6kg |
Approx. 7.4kg |
Approx. 10.6kg |
Approx. 21.7kg |
Approx. 36.2kg |
Supplied cable |
12-conductor flexible cable (2m) Cable end: 5 wires → Cable length is switchable to 5m(Option:UTMⅢ-L5) |
||||
Optionally available cable |
CATM351:12-conductor flexible cable (5m) Cable end: 5 wires CATM312:12-conductor flexible cable (10m) Cable end: 5 wires |
||||
CE marking certificatio |
EMC directives EN61326-1,EN61326-2-3 |
Permissible shaft end load *2
Measurement range |
±500Nm | ±1000Nm | ±2000Nm | ±5000Nm | ±10000Nm |
---|---|---|---|---|---|
RadialN | 300N | 400N | 500N | 1000N | 1200N |
ThrustN | 1800N | 3000N | 4500N | 7000N | 11000N |
RadialN (R, RC, RK, RCK) |
200N | – | – | – | – |
ThrustN (R, RC, RK, RCK) |
1800N | – | – | – | – |
Option
Measurement range |
±500Nm | ±1000 Nm |
±2000 Nm |
±5000 Nm |
±10000 Nm |
---|---|---|---|---|---|
Key Groove | ○ | ○ | ○ | ○ | ○ |
Rotary encoder | ○ | ||||
Key groove & Rotary encoder |
○ | ||||
Centering location |
○ | ||||
Key groove & Centering location |
○ | ||||
Rotary encoder & Centering location |
○ | ||||
Key groove & Rotary encoder & Centering location |
○ |
*1 0.05 to 10Nm model can be changed to 60 pulses in 1 rotation specification. Contact us for more details.
*2 Radial N and Thrust N of permissible shaft end load are the values guaranteeing that influence for torque output is less than 0.03% when those loads apply.
*2 Radial N and Thrust N of permissible shaft end load are the values guaranteeing that influence for torque output is less than 0.03% when those loads apply.
View more about UTMⅢ Slip-ring-less rotating torque meter on main site